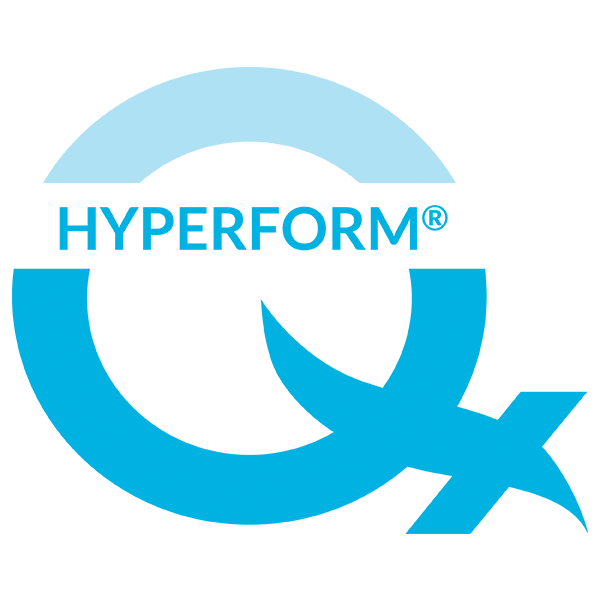
Hyperform® is a one-component, rapid-setting, high-early-strength patching material designed for repairing vertical and horizontal concrete and masonry structures.
Hyperform® is a one-component, rapid-setting, high-early-strength patching material designed for repairing vertical and horizontal concrete and masonry structures.
Hyperform® is a one component, rapid setting, high early strength patching material designed for repairing vertical and horizontal concrete and masonry structures.
Hyperform is supplied in 60 lb. (27 kg.) poly-lined bags.
One 60-lb. bag of Hyperform will yield approximately .48 cu. ft. and will cover 11.5 sq. ft. at a 1/2 in. thickness.
Prepare surface to be patched by removing all loose concrete by using an air or electric hammer. Next, sandblast or water blast surface to clean away all contaminants, such as oil, chemicals, or dust. Then rinse with potable water to remove all remaining dirt, sand and loose debris.
Mix Hyperform with clean potable water at a rate of 1.0 gallon per 60 pound bag. If needed, Hyperform can be extended with 3/8“ aggregate at a rate of 25 pounds per bag.
Quadex® warrants its products to be free of defects in material and workmanship. Within one year from purchase, if any Quadex product is proven defective, Quadex will replace said product or refund its purchase price at Quadex’s sole discretion. Quadex’s obligation shall be limited solely to such replacement or refund. There are no other warranties by Quadex, expressed or implied. There is no warranty if Quadex products are used contrary to Quadex’s written directions.
Avoid eye contact or prolonged contact with skin. Wash thoroughly after use. Persons using Hyperform should wear necessary eye protection, dust mask and rubber gloves. Read all product labels and technical literature.
Chimney Guard is a 100% solids epoxy/urethane hybrid designed to provide a highly flexible and securely bonded seal prepared to address heavy traffic loading, extreme freeze thaw and infiltration.
Chimney Guard is a 100% solids Epoxy/Urethane hybrid designed to provide a highly flexible and securely bonded seal prepared to address heavy traffic loading, extreme freeze thaw and infiltration.
Concrete: Existing concrete must be hydro blasted using a turbo tip at 4000psi until all loose concrete is removed. New concrete must be cured for 28 days prior to application of Chimney Guard. Abrasive blast, in accordance to SSPC-SP13/NACE 6, must be performed prior to application of Chimney Guard.
Steel: Near-White Blast SSPC-SP10/NACE 2. Sandblasting is required when applying Chimney Guard to manhole frame.
All surfaces must be clean and free from oil, grease and other contaminants!
Fill all voids and cracks greater that 1/8 inch with Quadex™ Hyperform™. Wait one hour before applying Chimney Guard. Quadex AluminaLiner will need a full 24-hour cure prior to the application of Chimney Guard. Quadex GeoKrete® and QM-1s™ will need a full 5-day cure prior to the application of Chimney Guard. When Quadex Structure Guard® has been used to line the manhole, Chimney Guard can be applied directly to Structure Guard within 8 hours, or as soon as Structure Guard has become tack free. After 8 hours, Structure Guard must be abraded with 80 grit sand paper before applying Chimney Guard.
All surfaces must be dry before applying Chimney Guard.
Use Acetone to clean tools.
Premeasured kit approximately 1.3 gallons. Store Chimney Guard at room temperature (70°F) in original container. Do not allow to freeze.
Structure Guard® – Water is a 100% solids epoxy coating made for plural component spray application. NSF 61 certified for pipe as small as 4″ diameter and tanks 50 gallons and larger.
Structure Guard® – Water is a 100% solids epoxy coating made for plural component spray application. NSF 61 certified for pipe as small as 4” diameter and tanks 50 gallons and larger. With a 25 minute pot life and extended re-coat time, Structure Guard – Water is the perfect product to coat long pipelines and large water tanks.
5 gallon buckets (15 gallon kit), 55 gallon drums (150 gallon kit)
25 minutes
4 hours at 70°F
Existing Concrete and Masonry
Substrates must be prepared in a manner that provides a uniform, sound, clean, neutralized surface with sufficient profile suitable for the specified coating. The substrate must be free of all contaminants, such as oil, grease, rust, scale or deposits and have a surface profile equivalent to a CSP3 to CSP5 in accordance with ICRI Technical Guideline No. 03732. This can generally be achieved by abrasive blasting, shot blasting, high pressure water cleaning, water jetting, acid etch, hot water/steam cleaning or a combination of methods.
New Concrete and Masonry
Substrates must be sandblasted to achieve a CSP4.
Steel / Metal
Near-White Blast SSPC-SP10/NACE 2
2 parts Structure Guard®-Water Part A to 1 Part Structure Guard®-Water Part B
Pre Heat: 80 Degrees Fahrenheit Part A and Part B (No solvent used in thinning). Plural Component Equipment Spray Equipment: Graco XM50 or Graco XP70. Gun Setup: Can be applied at 40-60 psi at the gun using a 517 tip. Mil Thickness: Apply 40-60 mils per. Re-coat Time: Must be re-coated with in 12 After 12 hours the first coat must be abraded.
Acetone or MEK
Structure Guard – Water contains Amines that can be harmful to skin and eyes. If contact with skin or eyes rinse thoroughly with water. See SDS for full instructions. Always consult a medical physician with concerns.
Structure Guard® is a 100% solids, high-build epoxy coating formulated to provide long-term corrosion protection and structural enhancement for manholes, pump stations, treatment plants or any wastewater infrastructure subject to high levels of corrosion and/or abrasion to include both municipal and industrial applications.
Structure Guard® is a 100% solids, high-build epoxy coating formulated to provide long-term corrosion protection and structural enhancement for manholes, pump stations, treatment plants or any wastewater infrastructure subject to high levels of corrosion and/or abrasion to include both municipal and industrial applications. Structure Guard sets fast for a quick return-to-service in the most aggressive and turbulent environments. It finishes smooth to enhance flow and is utilized as an interior or exterior pipe lining.
Heated Plural Airless Spray Units
Minimum Output 5000 psi
Product Hose: – Optimum I.D. 0.375 – 0.5 inch
Re-coat — 2 hours
Light Loading — 1 hour
Immersion — 4 hours
Full Chemical Cure — 24 hours
40°F (4°C) 20 minutes
70°F (24°C) 10 minutes
92°F (33°C) 5 minutes
Structure Guard is available in 5 gallon pails and 55 gallon drums.
Structure Guard will yield theoretical coverage of 20 sq. ft per gallon @ 80 mils thickness. Actual surface coverage will depend on substrate porosity and roughness. A wet film thickness gauge may be used to determine actual coating thickness.
With Structure Guard®, only 1 coat is needed to attain finished thickness. If additional coats are called for they must be applied before the previous coat has completely cross-linked, typically for
2 hours @ 70°F (higher temperatures/humidity will shorten this window). If re-coating is needed, brush blast before applying the next coat. Before re-coating, clean and dry surface thoroughly to remove all contamination, including amine blush or condensation. Small areas may be abraded by sanding or wire brushing.
The same requirements apply when overlapping seams of adjacent coating sections to create a continuous protective film. If the coating surface to be overlapped at the seam cannot be brush blasted, use a non-impact means, such as power brushing or sanding, to create adequate mechanical profile.
Coating performance is largely determined by the degree of surface preparation. MORE IS BETTER.
EXISTING CONCRETE AND MASONRY substrates must be prepared in a manner that provides a uniform, sound, clean, neutralized surface with sufficient profile suitable for the specified coating. The substrate must be free of all contaminants, such as oil, grease, rust, scale or deposits and have a surface profile equivalent to a CSP3 to CSP5 in accordance with ICRI Technical Guideline No. 03732. This
can generally be achieved by abrasive blasting, shot blasting, high pressure water cleaning, water jetting, acid etch, hot water/steam cleaning or a combination of methods.
NEW CONCRETE AND MASONRY SUBSTRATES must be profiled to achieve a CSP4.
STEEL surfaces may require “Solvent Cleaning” (SSPC-SP 1) to remove oil, grease and other soluble contaminants. Chemical contaminants may be removed according to SSPCSP 12/NACE No. 5. Identification of the contaminants, along with their concentrations, may be obtained from laboratory and field tests as described in SSPC-TU 4 “Field Methods for Retrieval and Analysis of Soluble Salts on Substrates”. Surfaces to be coated should then be prepared according to SSPC-SP 5/NACE No.1 “White Blast Cleaning” for immersion service or SSPC-SP 10/NACE No. 2. “Near White Blast Cleaning” for all other service. In certain situations, an alternate procedure may be to used such as high (>5,000 psi) or ultrahigh (>10,000 psi) pressure water cleaning or water cleaning with sand injection. The resulting anchor profile shall be 2.5-5.0 mils and be relative to the coating thickness specified.
Quadex® warrants its products to be free of defects in material and workmanship. Within one year from purchase, if any Quadex product is proven defective, Quadex will replace said product or refund its purchase price, at Quadex’s sole discretion. Quadex’s obligation shall be limited solely to such replacement or refund. There are no other warranties by Quadex, expressed or implied. There is no warranty if Quadex products are used contrary to Quadex’s written directions.
Flex Guard®-FM flexible fiber-reinforced epoxy mastic is designed to be applied to metal and concrete substrates that experience movement. With a 100-150% elongation, it is ideal for freeze/thaw and structures that experience temperature fluctuation.
Flex Guard™-FM flexible fiber reinforced epoxy mastic is designed to be applied to metal and concrete substrates that experience movement. With a 100-150% elongation, it is ideal for freeze/thaw and structures that experience temperature fluctuation. Also used in the STAG Crack Injection System to cap cracks.
600×600 ml cartridge
1:1 in premeasured cartridge
Mechanical grinding is required prior to application of Flex Guard™-FM. Use 80 grit diamonds to achieve a CSP#3 profile. When used as a mastic: Hydro Blast at 5000 psi. When used as a crack sealer: Use grinder to remove any loose concrete. Smooth edges of crack. Plow crack out with a air blower. Substrate must be free of grease, standing water and other contaminants that may impede adhesion. Always check the surface for any bond inhibitors prior to application.
Remove nut and plug from the cartridge. Attach static mixing tip to cartridge. Place cartridge in dispensing gun. Pull trigger on dispensing gun and burn 2 oz into a cup. As a Mastic: Apply directly to substrate. Using a putty knife, smooth to desired finish. As a crack filler: Apply epoxy directly into crack until level with the floor. Allow to dry 2 hours before top-coating. When being used in conjunction with BGFL76: Use a putty knife spread Flex Guard-FM over the crack to cap it in epoxy leaving a 3-inch space for epoxy ports to be applied. Apply Flex Guard-FM to the outside edge of the port. No Flex Guard-FM should block the center passage of the port.
Acetone or MEK
Flex Guard-FM contains Amines that can be harmful to skin and eyes. If contact with skin or eyes rinse thoroughly with water. See SDS for full instructions. Always consult a medical physician with concerns.
Quadex® GeoKrete® geopolymer is formulated to provide corrosion-resistant protection in a high hydrogen sulfide environment, restore structural integrity and eliminate the infiltration of groundwater in deteriorated structures.
Quadex GeoKrete geopolymer is formulated to provide corrosion resistant protection in a high hydrogen sulfide environment, restore structural integrity and eliminate the infiltration of groundwater in deteriorated structures. GeoKrete is a factory blended, one-component (just add water), eco-friendly, micro-fiber reinforced geopolymer mortar synthesized from reactive SiO2 and Al2O from industrial byproducts, enhanced with monocrystalline quartz aggregate. The GeoKrete geopolymer reaction mechanism is alkali-activated polycondensation which yields superior physical properties and chemical resistance. It can be applied in one pass up to several inches thick on horizontal or vertical surfaces by low pressure spraying or spin cast application process.
GeoKrete geopolymer is supplied in 60 lb. | 27.2 kg. poly- lined bags or 1,000 lb. | 454kg super sacks.
One 60 lb. | 27.2 kg bag of GeoKrete geopolymer will yield approximately 0.45 cu. ft. | 0.013 cu. m. and will cover 10.8 sq. ft. | 1.0 sq. m. at a 1/2-inch | 12.7 mm thickness.
Prepare surface to be patched by removing unsound concrete, dirt, dust, oil and other debris using high pressure (3,500 PSI | 241.3 bar) water blasting. Stop active infiltration. Then rinse with potable water to remove all remaining dirt, sand and loose debris. This will provide a clean, damp surface to allow for a good bond.
Use approximately 0.49 to 0.59 gallons | 1.85 to 2.23 liters of potable water per 60 lb. | 27.2 kg bag of GeoKrete geopolymer. For 1,000 lb. | 454 kg. supersack use approximately 8.0 to 9.5 gallons | 30.3 to 36 liters of potable water. First add water to mixer, start the mixer and add GeoKrete geopolymer until mortar is completely mixed. Once all geopolymer material and water has been added to mixer, it needs to mix for approximately five (5) minutes prior to being transfered into the material hopper. Once fully mixed, additional water may be added, as approved by Quadex, should it be necessary for proper consistency.
Apply GeoKrete geopolymer by low pressure spraying or the spin cast application process on horizontal or vertical surfaces to a monolithic minimum thickness of 1/2-inch | 12.7 mm for a protective layer to new or non-corroded infrastructure and 1.0-inch | 25.4 mm for structural restoration of existing infrastructure.
Cure in accordance with manufacturer’s recommendations.
Quadex warrants its products to be free of defects in material and workmanship. Quadex will replace any product proved to be defective when applied in accordance with manufacturer’s instructions. Quadex’s obligation shall be limited solely to such replacement. There are no other warranties by Quadex, expressed or implied.
Avoid eye contact or prolonged contact with skin. Wash thoroughly after use. Persons using Quadex GeoKrete geopolymer should wear necessary PPE consisting at minimum of eye protection, dusk mask and rubber gloves. Read all product labels and technical literature prior to use.
Structure Guard®-FM is a 100% solids epoxy mastic used to protect new infrastructure and to rehabilitate existing, damaged, infrastructure.
Structure Guard®-FM is a 100% solids epoxy mastic used to protect new infrastructure and to rehabilitate existing, damaged, infrastructure. Structure Guard-FM is best applied using a trowel.
Net Weight — 2.5 lbs (usable material)/cartridge
15 lbs (usable material)/case (6 cartridges)
Sq. ft. per gallon 250 mils 6.4 sq. ft.
Sq. ft. per 6 cartridge case 250 mils 9.12 sq. ft.
Concrete/Brick: Substrate surface must be Hydro Blasted at 5000 psi, removing any loose concrete or other material. Must be free of grease and oil. ALL SURFACES MUST BE DRY, CLEAN AND FREE FROM OIL, GREASE AND OTHER CONTAMINANTS!
Color – Green
Solids – 100% (no solvents)
Volatile Organic Compounds (VOCs) – 0
Thickness – 125 to 250 mils per coat
Number of Components – 2
Re-coat – 2 hours
Water Contact – 4 hours
Final Cure – 24 hours
Must be abraded with the equivalent of 36 grit sand paper after 24 hrs.
70°F
24 months unopened
10 minutes at 70°F (21°C)
2 to 1 in prepackaged cartridge. Use with 600 mil x 300 mil cartridge dispenser. Use only the material that the job requires, leaving virtually no wasted material.
Directly applied to substrate from static mixing tip. Use trowel or putty knife to smooth material.
Acetone. REFER TO SAFETY DATA SHEET FOR SAFETY AND HEALTH INFORMATION.
No harmful VOCs or odors. Disposable packaging and minimal waste.
Structure Guard®-RS is a 100% solid, high-build epoxy coating formulated to provide long-term corrosion protection and structural enhancement. Structure Guard-RS sets fast for a quick return-to-service in the most aggressive and turbulent environments.
Structure Guard®-RS is a 100% solid, high-build epoxy coating formulated to provide long-term corrosion protection and structural enhancement for manholes, pump stations, treatment plants or any wastewater infrastructure subject to high levels of corrosion and/or abrasion. Structure Guard-RS sets fast for a quick return-to-service in the most aggressive and turbulent environments. It finishes smooth to enhance flow and is utilized as an interior or exterior pipe lining. It is also ideal for invert repairs.
5 gallon kit
600ml x 300ml cartridge
Structure Guard-RS will yield theoretical coverage of 20 sq. ft per gallon @ 80 mils thickness. Actual surface coverage will depend on substrate porosity and roughness. A wet film thickness gauge may be used to determine actual coating thickness.
Re-coat Window — 2 hours
Immersion (Aqueous) Service — 1.5 hours
9 mins @ 77°F
With Structure Guard®-RS, only 1 coat is needed to attain finished thickness. If additional coats are called for they must be applied before the previous coat has completely cross-linked, typically for 2 hours @ 72°F (higher temperatures/humidity will shorten this window). If re-coating is needed, brush blast before applying the next coat. Before re-coating, clean and dry surface thoroughly to remove all contamination, including amine blush or condensation. Small areas may be abraded by sanding or wire brushing.
The same requirements apply when overlapping seams of adjacent coating sections to create a continuous protective film. If the coating surface to be overlapped at the seam cannot be brush blasted, use a non-impact means, such as power brushing or sanding, to create adequate mechanical profile.
Coating performance is largely determined by the degree of surface preparation. MORE IS BETTER.
EXISTING CONCRETE AND MASONRY substrates must be prepared in a manner that provides a uniform, sound, clean, neutralized surface with sufficient profile suitable for the specified coating. The substrate must be free of all contaminants, such as oil, grease, rust, scale or deposits and have a surface profile equivalent to a CSP3 to CSP5 in accordance with ICRI Technical Guideline No. 03732. This can generally be achieved by abrasive blasting, shot blasting, high pressure water cleaning, water jetting, acid etch, hot water/steam cleaning or a combination of methods.
NEW CONCRETE AND MASONRY SUBSTRATES must be sandblasted, or hydro blasted at 700psi 4gpm, to achieve a CSP4.
STEEL surfaces may require “Solvent Cleaning” (SSPC-SP 1) to remove oil, grease and other soluble contaminants. Chemical contaminants may be removed according to SSPCSP 12/NACE No. 5. Identification of the contaminants, along with their concentrations, may be obtained from laboratory and field tests as described in SSPC-TU 4 “Field Methods for Retrieval and Analysis of Soluble Salts on Substrates”. Surfaces to be coated should then be prepared according to SSPC-SP 5/NACE No.1 “White Blast Cleaning” for immersion service or SSPC-SP 10/NACE No. 2. “Near White Blast Cleaning” for all other service. In certain situations, an alternate procedure may be to used such as high (>5,000 psi) or ultrahigh (>10,000 psi) pressure water cleaning or water cleaning with sand injection. The resulting anchor profile shall be 2.5-5.0 mils and be relative to the coating thickness specified.
Quadex® warrants its products to be free of defects in material and workmanship. Within one year from purchase, if any Quadex product is proven defective, Quadex will replace said product or refund its purchase price, at Quadex’s sole discretion. Quadex’s obligation shall be limited solely to such replacement or refund. There are no other warranties by Quadex, expressed or implied. There is no warranty if Quadex products are used contrary to Quadex’s written directions.
I&I Guard® is a two-part polyurethane grout used to stop high-flow infiltration. It has an easy injection method creating a curtain of grout on the outside of underground structures. Super fast cure allows for immediate reduction in infiltration. It’s best when used in conjunction with Quadex® Repair Materials rehab systems.
I&I Guard® is a two-part polyurethane grout used to stop high flow infiltration. Easy injection method creating curtain of grout on the outside of underground structures. Super fast cure allows for immediate reduction in infiltration. Best when used in conjunction with Quadex® Repair Materials rehab systems.
Case of (6) 300ml x 300ml or 600ml x 600ml cartridges
Store between 40°F and 100°F.
Drill 5/8” hole completely through the structure. Remove nut from cartridge. Slide nut onto static mixing tip. Insert static mixing tip into the drilled hole and insert cartridge into the Quadex® OneGun®. Remove cap plug from cartridge and hold the Quadex OneGun upright. Attach cartridge to static mixing tip by tightening the nut. Pull trigger on Quadex OneGun to dispense grout. Continue to pull trigger until the cartridge is empty or until the OneGun automatically seizes.
Always use safety glasses and protective clothing including gloves when using this product.
Dispose of cartridge in adherence with local regulations.